Small / R & D VIM Furnaces
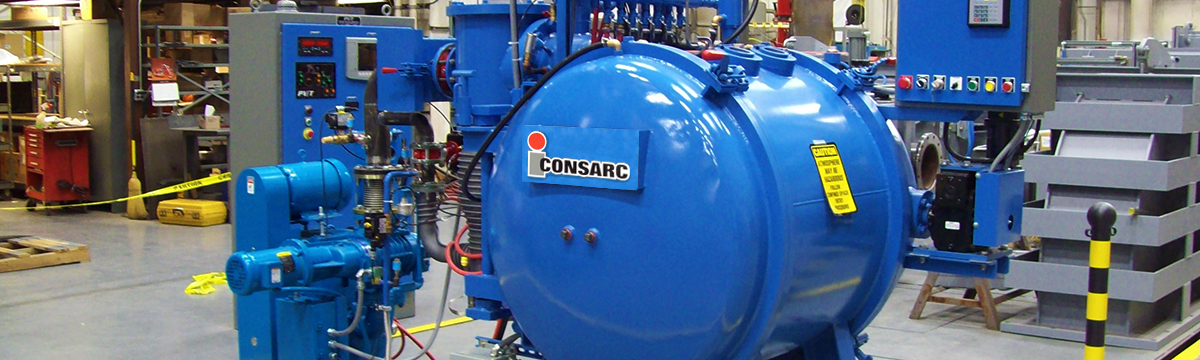
Small / R & D VIM Furnaces
Smaller VIM furnaces are commonly used to start a company in the business of producing vacuum induction melted materials, or for research and development efforts into new alloys and processes. A wide variety of configurations are available to match customer requirements.
Features
• Wide variety of furnace configurations available; furnaces are custom engineered and designed specifically for individual user’s process
• Can utilize billet, revert or virgin charge material in multiple charging systems
• Controls can be provided to customer’s specifications, from simple PLC-based terminal to full PC data logging
Tech Specs
Multiple Charging Systems:
• Overmelt chargers for primary bucket charging of high density charge materials, temperature probe insertion, and sample taking
• Cup chargers are available for charging of small pieces and fines, typically for late alloy additions
• Other charging system configurations are available
Vacuum System:
• Three stage vacuum pumping system incorporating oil sealed rotary pumps or dry type screw pumps, roots type mechanical blowers, and oil vapour booster pumps for finalizing vacuum levels in the 10-3 Torr range
• Oil wetted vacuum filters for control of pyrophoric additions such as NiMg, or dry type vacuum filters if these elements are not planned to be used
• State-of-the-art safety systems incorporating overpressure relief valves and argon purging
Mold Pouring:
• Most units are direct pour, or utilize a small pour box above each mold
• Hot tundish insertion via a charger configured to insert an externally preheated refractory tundish into the pour position within a few minutes is available
Controls:
• Simple PLC-based controls with touchscreen OIT are common
• Computerized control and SCADA systems may be implemented
• TV cameras on remotely actuated site ports for remote operation are available but not typically required
Furnace Layout
Most small / R&D VIM furnaces are door-mounted designs, though this varies depending on the layout of the equipment and the available space and access routes for loading / unloading of molds and induction furnaces.